The 2012 IEEE ECTC conference was held, as it always is, over Memorial Day weekend this year in San Diego. Attendance was an outstanding 1200+.
The executive committee, which is responsible for all content, is shown below. (Click on any images to enlarge them.)
[Back row: Steve Bezuk, Pat Thompson, Wolfgang Sauter, Beth Kesser (winner of the IFTLE name the packaging experts contest !), Bill Moody, Sunil Peking, Alan Huffman, Tom Reynolds Front row: Eric Perfecto, Jean Trewhella, Kitty Pearsall, Dave McCann, Rajen Dias, Lisa Renzi]
The committee gave special thanks to two wives who have been helping with registration and anything else the conference needed for over a decade -- Lynn Reynolds and Nadine Bezuk:
IEEE CPMT AWARDS
The theme of this year's meeting was "going on safari" (I assume tied to the San Diego Zoo) so that's a safari hat on Ricky's head in case you're wondering.
This year's award winners included:
IEEE CPMT Field Award to Dr. Mauro Walker (Motorola - Retired)
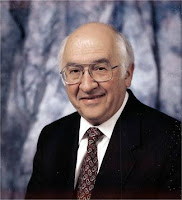
He is the previous recipient of the IEEE's Special Manufacturing Technology Award and the Society for Manufacturing Engineers' "Total Excellence in Electronic Manufacturing Award." Walker is an IEEE fellow and founder of the IEEE International Electronic Manufacturing Technology Symposium (IEMT).
Having worked on technology introduction programs with Motorola during this time, I can tell you that this is a well deserved award. There was no one introducing technology like bumping and chip scale packaging into consumer products better or earlier than Motorola in those days. Congrats Mauro!
IEEE CPMT Dave Feldman Award to Dr. Phil Garrou (Microelectronic Consultants of NC)
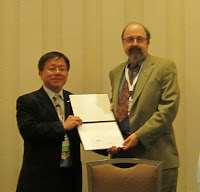
Sustained Technical Contribution Award - Tseung-Yuen Tseng (Chiao-Tung Univ Taiwan)
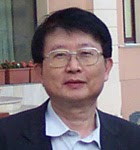
Exceptional Technical Achievement Award - Andrew Tay - National Univ of Singapore
Electronics Manufacturing Technology Award - Chin Lee - Univ of California
Outstanding Young Engineer Award - Mudasir Ahmad - Cisco
IEEE Fellows - Mao Jun Fa (china), Yogendra Joshi (USA), Pradeep Lall (USA), Mike Li (USA), Anthony Oates (Taiwan), William Palmer (USA), Enboa Wu (China)
For all the latest on 3DIC and advanced packaging stay linked to IFTLE....................